|
ACCESS THE FULL ARTICLE
No SPIE Account? Create one
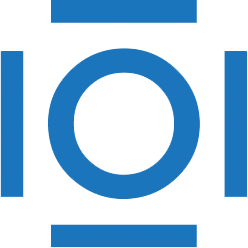
CITATIONS
Cited by 2 scholarly publications.
Acoustic emission
Sensors
Spindles
Abrasives
Calibration
Defect detection
Motion measurement