|
ACCESS THE FULL ARTICLE
No SPIE Account? Create one
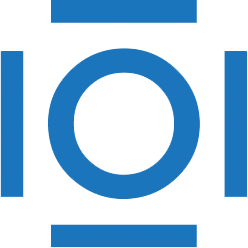
CITATIONS
Cited by 2 scholarly publications.
Actuators
Composites
Electrodes
Finite element methods
Standards development
Ferroelectric polymers
Polymers