|
ACCESS THE FULL ARTICLE
No SPIE Account? Create one
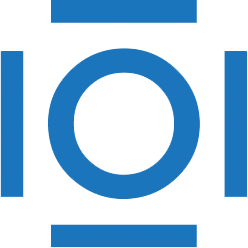
CITATIONS
Cited by 2 patents.
Ceramics
Cladding
Resistance
Particles
Laser processing
Temperature metrology
Composites