|
ACCESS THE FULL ARTICLE
No SPIE Account? Create one
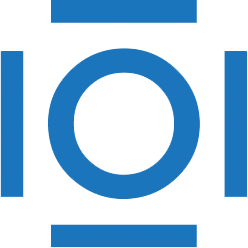
CITATIONS
Cited by 3 scholarly publications.
Semiconducting wafers
Overlay metrology
Lithography
Distortion
Scanners
Plasma enhanced chemical vapor deposition
Semiconductors