|
ACCESS THE FULL ARTICLE
No SPIE Account? Create one
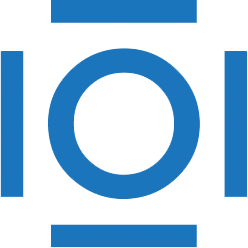
CITATIONS
Cited by 4 scholarly publications.
Inspection
Cameras
Image processing
Imaging systems
Light sources and illumination
Discrete inspection
Machine vision