|
ACCESS THE FULL ARTICLE
No SPIE Account? Create one
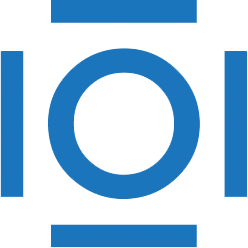
CITATIONS
Cited by 2 scholarly publications.
Optical proximity correction
Photomasks
Manufacturing
Printing
Resolution enhancement technologies
Semiconducting wafers
Defect detection