|
ACCESS THE FULL ARTICLE
No SPIE Account? Create one
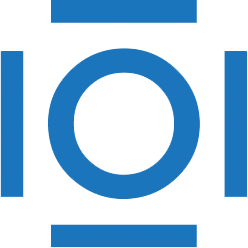
CITATIONS
Cited by 6 scholarly publications.
Optical proximity correction
Photomasks
Metals
Double patterning technology
Resolution enhancement technologies
Lithography
Manufacturing